Understanding the Low Pressure Casting Process: A Comprehensive Guide
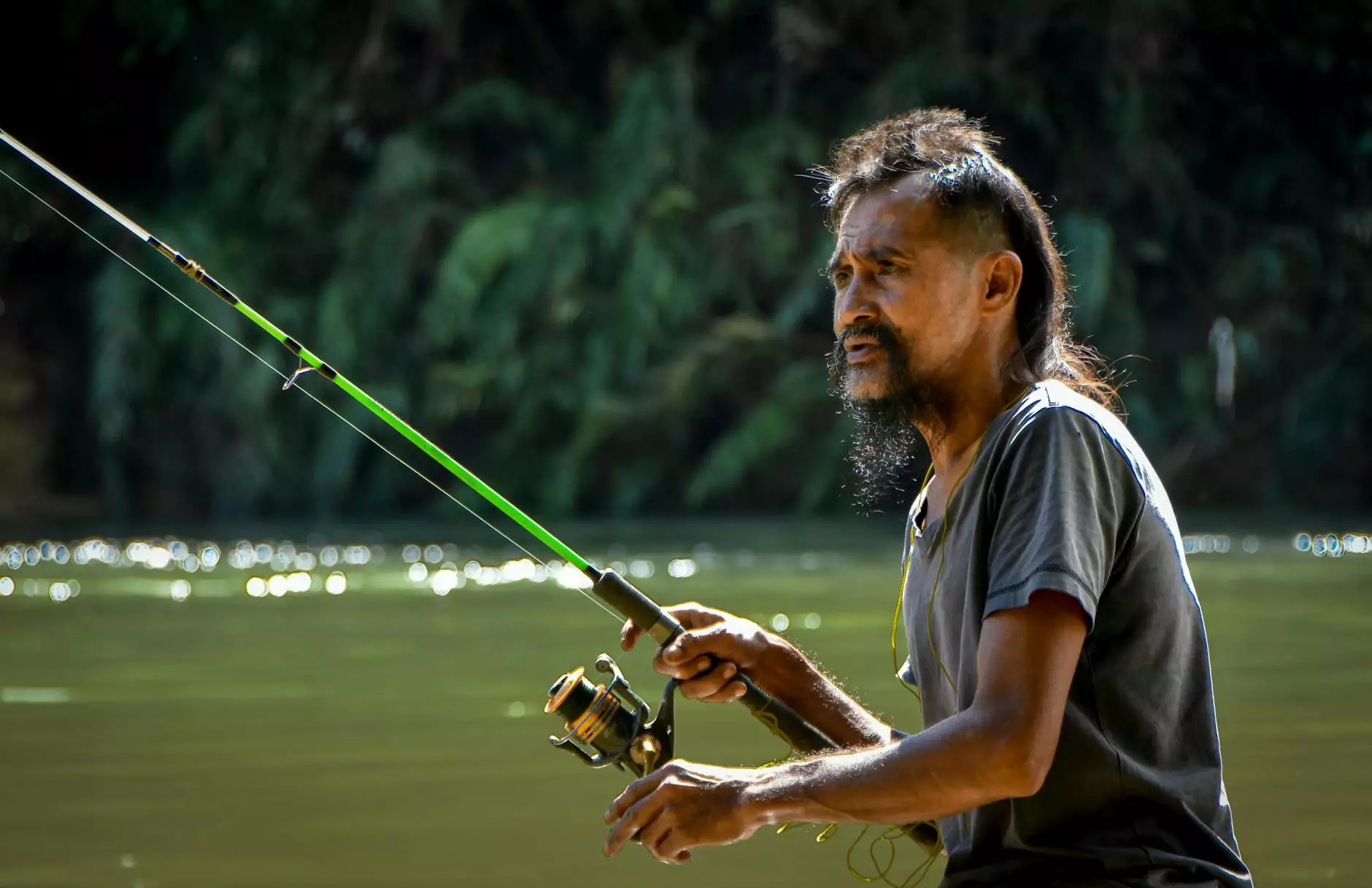
The low pressure casting process is a revolutionary technique in the field of metal casting that has gained significant traction due to its efficacy and precision. This method is not only pivotal for the manufacturing industry but also plays a crucial role in product design and 3D printing solutions available at Arti90.com. In this extensive guide, we will explore the nuances of low pressure casting, its advantages, applications, and how it integrates within the broader context of business and innovation.
What is the Low Pressure Casting Process?
Low pressure casting is a process that involves the use of low atmospheric pressure to fill a mold with molten metal. This technique allows for the creation of intricate shapes and details that are difficult to achieve through conventional casting methods. The low pressure ensures that the metal fills the mold cavity completely, reducing the likelihood of defects such as air pockets or voids.
How Does the Low Pressure Casting Process Work?
The low pressure casting process operates as follows:
- Mold Preparation: The first step involves creating a permanent mold, often made from steel or iron, designed to withstand the pressures involved in casting.
- Metal Melting: The molten metal, typically aluminum or magnesium, is melted in a furnace and carefully maintained at the required temperature.
- Vacuum Creation: A vacuum is created in the mold to ensure that the environment is free of air, which is crucial for achieving high-quality castings.
- Metal Pouring: Under low pressure, the molten metal is introduced into the mold. The pressure, usually between 0.5 to 1 bar, assists in pushing the metal into every intricate detail of the mold.
- Cooling: After the molten metal fills the mold, it is allowed to cool, solidifying into the desired shape.
- Mold Removal: Once cooled, the mold is removed to reveal the cast product, ready for further finishing or assembly.
Advantages of the Low Pressure Casting Process
The low pressure casting process offers several notable advantages, making it a preferred choice for many manufacturers:
- Reduced Defects: The controlled nature of low pressure reduces the chances of defects, such as air bubbles and shrinkage cavities, leading to high-quality finished products.
- Cost-Effectiveness: Less waste material and lower energy consumption make this method more cost-effective compared to traditional casting processes.
- Design Flexibility: The ability to cast complex geometries allows designers more creative freedom in product development.
- Superior Surface Finish: Products produced via low pressure casting often require less finishing work due to the smooth nature of the casting.
- Rapid Production Rates: High production rates can be achieved, allowing businesses to meet demand efficiently.
Applications of Low Pressure Casting
The versatility of the low pressure casting process makes it applicable in a variety of industries, including:
- Aerospace: Used for creating lightweight yet strong components.
- Automotive: Commonly utilized in the production of engine blocks, transmission cases, and decorative elements.
- Electronics: Employed for housing components that require intricate shapes for optimal performance.
- Medical Devices: Essential in the manufacturing of precision instruments where reliability is paramount.
Integrating Low Pressure Casting with Product Design
At Arti90.com, the integration of the low pressure casting process in product design has transformed how businesses innovate. It allows designers to create prototypes rapidly, test them, and refine their designs before entering full-scale production. This iterative process is essential in today's fast-paced market where time-to-market can be a critical factor in a product's success.
Enhancing Product Aesthetics
One of the most significant advantages of using low pressure casting in product design is the ability to achieve stunning aesthetics. The process allows for:
- Intricate Designs: Complex shapes and forms can be realized, enhancing visual appeal.
- Custom Finishes: The nature of the casting process allows for various surface finishes, which can be tailored to meet specific design requirements.
Prototyping Speed and Efficiency
The speed at which prototypes can be created using the low pressure casting process facilitates innovation in design. Instead of waiting for traditional manufacturing methods, designers can quickly produce and evaluate prototypes, making adjustments in real-time based on performance and aesthetic evaluations.
3D Printing and Low Pressure Casting: A Perfect Match
The intersection of 3D printing and low pressure casting represents a groundbreaking approach in manufacturing. 3D printing can be utilized for creating the initial models or molds needed for low pressure casting. This synergy offers several advantages:
- Rapid Model Development: 3D printing allows for quick iterations and adjustments to designs before moving on to casting.
- Cost Reduction: Creating molds through 3D printing can significantly reduce costs compared to traditional mold-making techniques.
- Precision and Detail: 3D printing technologies can achieve high precision, ensuring molds fit perfectly and produce accurate castings.
Challenges and Considerations
While the low pressure casting process presents numerous benefits, there are still challenges and considerations businesses should be aware of:
- Material Limitations: Not all metals can be low pressure cast, which may limit some applications.
- Investment Costs: Initial investment in equipment and technology can be significant, although operational costs may reduce over time.
- Process Control: Maintaining the necessary temperature and pressure conditions is critical for quality control and requires skilled operators.
The Future of Low Pressure Casting in Business
The future of the low pressure casting process looks promising as industries continue to evolve. As technology advances, improvements in automation and processing capabilities will further enhance the efficiency and effectiveness of low pressure casting. Companies like Arti90.com are at the forefront of this trend, integrating the latest innovations into their product design and manufacturing strategies.
Sustainability and Environmental Impact
Another crucial aspect of the future of low pressure casting is its potential for sustainability. With growing environmental concerns, businesses are increasingly looking for methods that reduce waste and energy consumption. Low pressure casting is inherently more efficient, producing less scrap metal and requiring less energy than many traditional methods.
Embracing New Technologies
As new technologies emerge, the integration of artificial intelligence and automation in the low pressure casting process may redefine traditional practices. Companies must stay adaptable, ready to incorporate enhancements that can lead to better efficiency, quality, and sustainability in their production processes.
Conclusion
In conclusion, the low pressure casting process is an invaluable approach within modern manufacturing that offers practicality, precision, and extraordinary potential for innovation. From enhancing product design to optimizing production efficiency, this method is proving indispensable across various industries. Businesses looking to leverage the benefits of low pressure casting should consider how it can transform their design and manufacturing practices, ensuring they remain competitive in an ever-evolving market landscape. For more information on how we can assist you with product design and innovative manufacturing solutions, visit us at Arti90.com.