The Power of Injected Molded Plastic in Modern Business
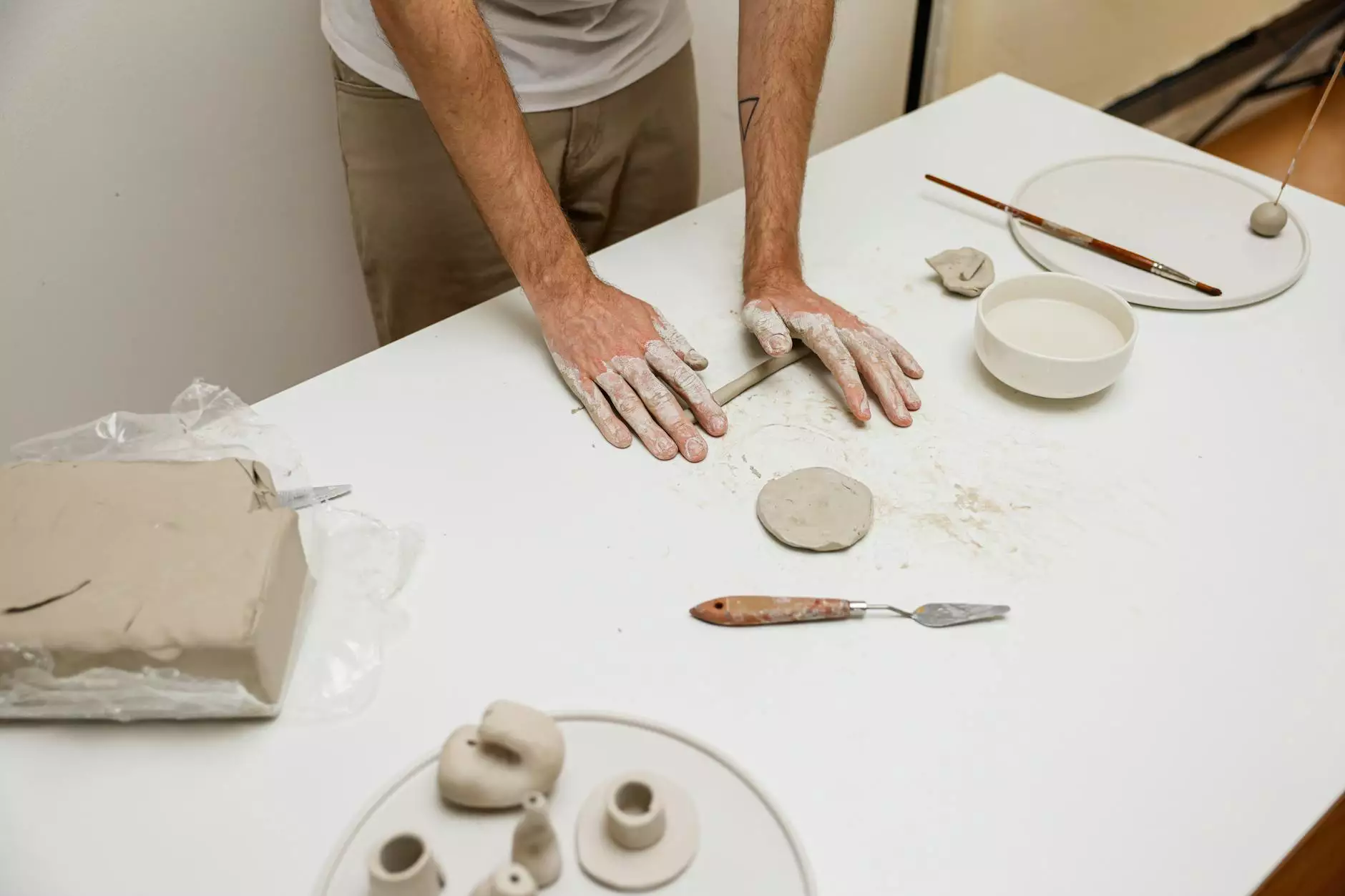
In today's competitive business landscape, companies strive for efficiency, durability, and cost-effectiveness. One of the key technologies that contribute significantly to achieving these goals is injected molded plastic. This sophisticated manufacturing process not only enhances product quality but also meets the diverse demands of various industries. In this article, we will dive deep into the intricacies of injected molded plastic, its benefits, applications, and impact on the business domain.
What is Injected Molded Plastic?
Injected molded plastic is a manufacturing process that involves the injection of molten plastic into a pre-designed mold to create specific shapes and parts. The process begins with heating raw plastic material until it is in a liquid state, which is then injected through a nozzle into a mold cavity. Once cooled, the plastic solidifies, taking the shape of the mold. This method is especially favored for its ability to produce intricate designs with high precision and consistency.
Why Choose Injected Molded Plastic?
The choice of injected molded plastic brings about a myriad of advantages, including:
- Efficiency: The production process is remarkably fast, reducing lead times for product development.
- Cost-Effectiveness: While the initial setup costs can be high, the long-term savings from mass production make it economical.
- Design Flexibility: Complex geometries and detailed features can easily be achieved.
- Material Variety: A wide range of plastic materials, such as polycarbonate, polypropylene, and ABS, can be used based on application needs.
- Sustainability: Many plastics today are recyclable, making this method more environmentally friendly than traditional materials.
The Process of Injected Molded Plastic
Understanding the process of injected molded plastic is crucial for businesses looking to incorporate it into their operations. The following steps outline the typical manufacturing process:
1. Material Selection
The first step is to select the appropriate plastic material. Factors influencing material choice include strength, flexibility, and thermal resistance. Commonly used materials include:
- Polypropylene: Known for its chemical resistance and lightweight nature.
- ABS: Offers strength and impact resistance, making it ideal for consumer goods.
- Polycarbonate: Renowned for its high impact resistance and clarity.
2. Mold Creation
The next step involves fabricating the mold, which is a critical component in the injected molded plastic process. This mold is usually made from steel or aluminum and is designed to withstand high pressure and temperature. The quality of the mold directly influences the finished product's quality.
3. Melting the Plastic
Once the mold is ready, the selected plastic material is heated in a machine called an injection molding machine. The temperature is meticulously controlled to ensure the plastic achieves a molten state that allows it to flow smoothly into the mold.
4. Injection of Plastic
The molten plastic is then injected into the mold under high pressure. This pressure ensures that the plastic fills all corners of the mold, capturing the design's intricacies. The speed of injection can be adjusted based on the complexity and size of the part being manufactured.
5. Cooling and Ejection
After the injection, the plastic is allowed to cool within the mold for a pre-determined time. Once cooled, the plastic solidifies, and the mold is opened to eject the finished product. This step requires precision to avoid damaging the newly formed piece.
Applications of Injected Molded Plastic in Business
Injected molded plastic finds applications across various industries due to its versatility. Here are some predominant sectors where this manufacturing technique plays a vital role:
1. Automotive Industry
The automotive industry is one of the largest consumers of injected molded plastic parts. From dashboards and door panels to under-the-hood components, the lightweight and customizable nature of plastic aids in improving fuel efficiency and reducing overall vehicle weight.
2. Consumer Products
Everyday items like containers, toys, and household appliances often use injected molded plastic. The ability to produce large volumes of aesthetically pleasing and durable products makes it ideal for consumer goods.
3. Electronics
In the electronics industry, injected molded plastic is used for creating casings, connectors, and other components that require high precision and reliability. With the rise of smart devices, the demand for intricate molds has surged.
4. Medical Devices
In the medical field, injected molded plastic is crucial for producing various devices and disposable items, including syringes, surgical tools, and diagnostic equipment. The ability to meet strict regulatory standards is paramount, and this method allows consistent quality control.
The Benefits of Injected Molded Plastic for Businesses
Incorporating injected molded plastic into production can lead to significant business advantages:
1. Increased Production Speed
With advanced technology, this manufacturing method enables rapid production. Shorter production cycles mean that businesses can respond faster to market demands, maintaining a competitive edge.
2. Cost Savings
Although the setup costs can be high, the efficiency gained in mass production leads to reduced per-unit costs over time. This can translate into lower prices for consumers and higher margins for businesses.
3. Enhanced Product Quality
Businesses benefit from the high precision and consistency of molded parts. This quality control reduces defects and boosts customer satisfaction, ultimately enhancing brand loyalty.
4. Design Versatility
Injectable molded plastic allows for complex designs, offering businesses the flexibility to innovate and create products that stand out in the market.
Conclusion
In summary, the process of injected molded plastic presents an array of benefits for businesses seeking efficiency, cost-effectiveness, and quality in production. As industries continue to evolve, the demand for innovative manufacturing techniques like injected molding will only grow. By leveraging this technology, businesses can enhance their product offerings, meet customer expectations, and firmly establish their presence in the competitive marketplace.
The future of manufacturing lies in embracing advanced technologies like injected molded plastic, and companies need to stay informed and adapt to maintain their edge in the ever-changing business landscape.